The increasing global demand for seeds and grains, including seed corn and coffee beans, is a great opportunity for food processors to swell their revenue streams. To profit from these expanding markets, however, it is necessary to overcome some operational challenges. Here we identify those challenges, take a brief look at the technologies available to solve them, and explain why they can open doors to new business.
Big opportunities
One main reason for the booming popularity of seeds and grain – and for experts forecasting that sales will keep rising for years to come – is income growth in highly-populated developing nations. Every year, millions of more people find they have more money to spend on fast-moving consumer goods, including food. We have already seen seismic shifts in global consumerism because of economic growth in the earth’s most populous nation, China – and a recent study of 130 nations by economic analysts Focus Economics concluded that the world’s fastest-growing economy in the next five years will be that of the second-most populous, India.
The other main reason is the strengthening trend, particularly in developed nations, for healthy foods. Shoppers are increasingly looking for ‘clean-label’ products containing natural and nutritious ingredients, meaning that seeds and grains are being added to more foods than ever before. The best-selling examples of this are bread, bakery goods, and snack bars – all produced and consumed in vast quantities.
This is more than just a consumer fad or a blip on sales graphs. Market researchers forecast that during the next five years (and probably for much longer) the seed market will expand in annual value at a compound annual growth rate (CAGR) of 6-8%, rising from $63bn in 2020 to $85-90bn in 2025. In the same period, the grain market is expected to expand at a CAGR of about 6%, from $1,150bn to $1,556bn.
It is also worth remembering that grains include coffee beans, the source of one of the most widely-consumed drinks on the planet. Coffee prices reached new record highs in fall 2021, according to the World Coffee Organization. Though crop prices fluctuate because of weather conditions and variable yields, global demand is heading relentlessly upwards. Over the next five years, the annual value of the coffee bean market is expected to increase from $27bn at a CAGR of 6.7%. Much of this growth is being driven by rising demand for coffee capsules for home consumption and the opening of new franchise outlets such as CCD and Starbucks in many nations worldwide – including China and India.
Processing challenges
The key challenge facing processors is that new sales conquests are most likely to be made in export markets where product imperfections aren’t tolerated. This makes it more important than ever for processing lines to detect and eject foreign materials, defective products, cross-contaminated products, and products contaminated with mycotoxins. One mycotoxin, aflatoxin, is a real concern: this naturally-occurring poison can contaminate corn kernels intended for use in foods for human consumption and for pets, can all-too-easily prove lethal for cats and dogs, and yet is extremely difficult to detect.
Another challenge is that supply lags behind demand for many types of seeds and grains, but it can take years to plant more crops or enhance crop yields. This means processors must be more effective than ever at reducing food waste. It is no longer acceptable to use outdated sorting methods that discard large amounts of good product when rejecting bad products. Besides this, rejecting too much good-in-bad is throwing away potential income.
Yet another challenge, certain to become more widespread in the near future, is the emergence of genetically modified crops. Though the sale of GM foods will become more commonplace, they are unlikely to be welcomed by all consumers and may even be restricted or banned by some food regulators. This makes it essential for processors to prevent non-GM foods from becoming cross-contaminated with GM foods. It is also important to prevent cross-contamination, resulting in products containing unintended ingredients, such as soy, which are allergens.
Reasons for optimism
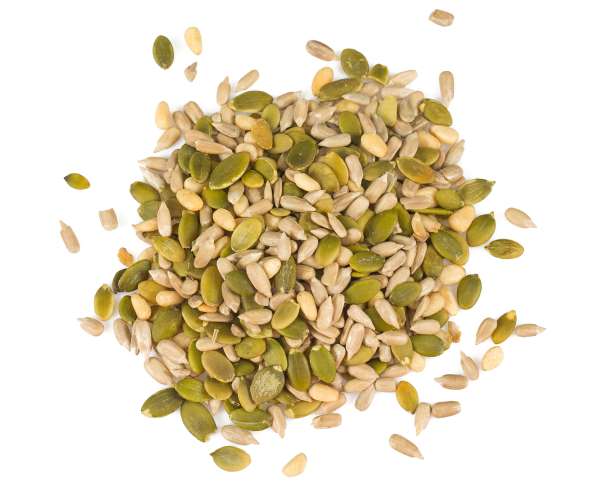
The good news is that all of these challenges – even the well-hidden threat posed by aflatoxin – can be met by using modern optical sorting machines. Industry-leader TOMRA Food offers a wide range of sorting solutions with various levels of sophistication to perform tasks of varying complexity. These machines are precisely calibrated for specific food applications and highly effective for many types of seed and grain. TOMRA machines are currently in operation around the world, sorting seed and feed corn, dry beans, lentils, chickpeas, dry peas, sunflower seeds, sesame seeds, pumpkin seeds, and roasted and unroasted coffee beans.
As well as enhancing food safety and product quality, TOMRA’s sorters deliver other benefits. These machines can grade to specification, increase removal efficiency, minimize false rejects, reduce or eliminate the need for manual intervention, and reduce or eliminate dependence on manual labor. The last point is especially important in developing nations where processors have traditionally relied on people rather than machines for sorting: whereas manual sorting is subjective, imperfect, and especially vulnerable to error when workers are tired or bored, automated sorters can work for hour after hour with superior accuracy, consistent standards, and unflagging efficiency.
What’s more, TOMRA’s machines are designed to be easy to keep clean, improve food hygiene, and be easily maintained, reducing line downtime. And because TOMRA’s machine platforms are robust, and their optical sensors are optimally located, sorting performance remains stable even when working conditions are dusty or subject to temperature extremes. Users find there is little or no degradation in sorting performance from the beginning of a shift to the end.
Wide-ranging sorting solutions
TOMRA’s sorters can inspect materials passing along the processing line according to their shape, color, structure, and biological characteristics. Which of these capabilities a machine possesses depends upon its technical specification, which will incorporate one or more ways of ‘seeing’: x-ray, high-resolution cameras, lasers, near-infrared (NIR) optical sensors, and TOMRA’s unique Biometric Signature Identification technology.
A variety of TOMRA machines are best-suited to seeds and grains: the Ixus Bulk, Zea, TOMRA 3C, and Nimbus BSI+, depending on the specific requirements.
The Ixus Bulk employs the latest x-ray and imaging technology to detect high-density foreign materials such as metal, stones, glass, and plastics.
The Zea, developed specifically for the seed corn industry, is an affordable sensor-based machine for sorting and grading ear corn husk, defects, disease, and size.
The TOMRA 3C combines high-resolution cameras with LED lighting plus laser or NIR units to remove foreign materials and product defects. This affordable and compact machine needs very little floor space and is loved by operators for its intuitive TOMRA ACT user interface. It works by pouring infeed materials into a hopper, then sending the feed to fall onto a vibration plate, which is spread evenly on an infeed chute. The materials then fall further into a detection area, where they are inspected by a dual laser and double-sided high-resolution cameras. In a matter of milliseconds, the intelligent inspection system rejects all defects. The acceptable product continues through the accept chute while the flaws are diverted via the reject chute.
The TOMRA 3C’s technologies result in numerous advantages. The dual laser-induced scattering results in superior glass and foreign material removal; the double-sided RGB cameras, combined with high intensity LED lighting, remove the subtlest color and shape defects; the high-speed ejection valve results in an exceptionally low rate of false rejects; intelligent auto-cleaning sustains the machine’s optimum performance; and the control interface, with a large touch screen showing application-specific tuning parameters, is easy for operators to use.
The Nimbus BSI+ uniquely combines lasers with NIR, visible spectroscopy, and TOMRA’s patented BSI+ scanner, which can detect objects’ biometric characteristics. This is also a free-fall machine: a feed shaker or hopper uniformly spreads the product over the free-fall chute, and after the product falls down to the inspection zone, it is scanned by cameras, lasers or BSI+, or a combination of these. A few milliseconds after this assessment is made, the defects are hit with a precise and powerful burst of air which sends them into the rejection zone while the good product continues its natural free-fall.
The Nimbus BSI+’s sophisticated technologies enable it to ‘see’ through a broader spectrum than other machines and to make more accurate decisions about the acceptability and grading of materials on the line. When equipped with the BSI+ scanner, the Nimbus is capable of detecting both color and chemical composition in the same pass, and of removing unwanted materials and product defects that would get past other sorters undetected – and when the Nimbus is equipped with the Detox laser module, it can also detect the presence of aflatoxin.
One of the businesses that have significantly benefitted from using the Nimbus BSI+ is Legumbres Selectas Sierra Nevada, a Spanish enterprise specializing in superior-quality pulses. The company’s CEO, Vicente Jiménez Blanes, says: “When I first saw this machine in operation, I knew it was exceptional, but I never imagined what it was capable of. The results are amazing: 99.9% product purity, and we have gone from processing 500 kilograms per hour to a total installed capacity of 5,000 kilograms per hour. The leap has been spectacular – installing the two Nimbus BSI+ machines is the best thing we’ve done in our company’s 57-year history.”
Another very satisfied user of the TOMRA 3C, and of the IXUS, is Termont & Thomaes, a successful business in the Netherlands which has been specializing in the sale of legumes, grains and seeds for more than 100 years. Ettienne Notschaele, process operator at the company’s plant in the town of Biervliet, commented: “With TOMRA’s machines, product quality and process quantities both increase. The result of using the TOMRA 3C and the IXUS is lower yield-loss and happier customers. We are also very happy with the guidance and help we get from TOMRA, whose team really put their heads together to come up with solutions which help us progress.”
Test and Demonstration Center
To ensure that operators extract each machine’s full potential, TOMRA provides on-site training for customers, as well as making technical experts accessible via a helpline. And with the recently-launched smartphone app TOMRA Visual Assist, TOMRA field service engineers and customers can work closely together even when they are thousands of miles apart. The engineer can provide detailed advice just as if standing right in front of the customer’s machine, and both the engineer and the customer can share documents or annotate images to clarify and explain directions.
Before getting to this stage, food producers are welcome to try-out TOMRA’s machines with their own infeed materials at TOMRA’s nearest Test and Demonstration Centre. There are 8 demo centers around the world in California, Chile, Belgium, Turkey, China, India, Japan and Ireland ).
Because of the COVID-19 pandemic, TOMRA also offers Online Demonstration Centers. These show tests via a live video link, with viewers encouraged to ask questions, make requests, and direct one of the cameras showing the proceedings. After the test’s conclusion, observers are provided with a video and report which quantifies results in detail.
These demonstrations mean that customers can be confident of a machine’s capabilities and suitability before deciding to invest in the technology. And it’s an investment that pays back in many ways: by differentiating better-equipped processors to gain them a competitive advantage; by opening new doors to markets which demand high product standards; and by protecting that most valuable of all business assets, brand reputation.