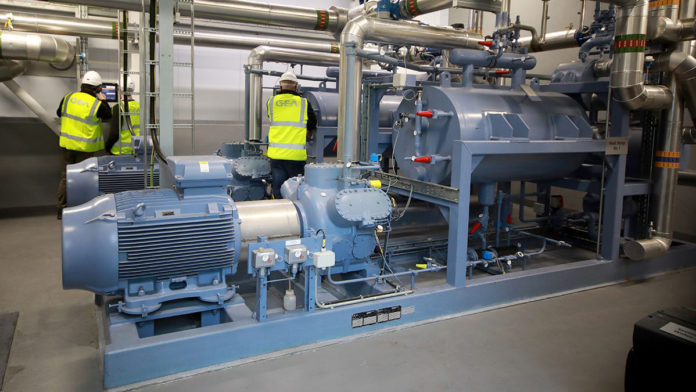
GEA, one of the world’s largest systems suppliers for the food, beverage and pharmaceutical sectors, has developed an air heating system for spray dryers that more than halves a plant’s consumption of fossil fuels and its associated carbon footprint. Based on high-temperature heat pumps, GEA AddCool is a patent-pending solution that can be integrated into an existing powder spray drying process. By cutting the plant’s overall heating requirements and costs, it makes production processes more sustainable.
Recovering waste energy
Spray drying is an industry standard that uses a constant stream of hot air to manufacture high-quality, stable powders. As the heaters supplying that flow usually operate on fossil fuels, they emit high levels of CO2. In a milk powder processing plant, the spray dryer is responsible for up to 70 percent of the overall heating requirements. But all the heat input into the process is eventually released at low temperatures as waste. The new GEA technology uses CO2 heat pump technology to recover waste heat from the exhaust air or other plant cooling processes. That energy is upgraded and used to warm the air in the spray dryer up to 120°C before feeding it into the dryer’s conventional heating setup.
Ulrik Lund Jakobsen, CEO of GEA Business Unit Powder & Thermal Separation Technologies says: “GEA AddCool technology is a real milestone in energy conservation. During the more than five-year development process, our experts in engineering, heat pump systems, spray drying and powder processing collaborated closely to overcome the challenges associated with designing the CO2 heat pump technology while simultaneously planning its integration into existing spray drying plants.”
Easy retrofitting into existing spray drying plants
Since the GEA AddCool heat pump system works as an addition to the native spray dryer air heating system without impairing plant throughput, final powder properties or quality, it can be easily retrofitted into conventional plants. Additionally, the option of reverting to the original setup during routine maintenance means that the spray dryer can continue powder production uninterrupted.
The GEA AddCool system has undergone extensive trials at the GEA testing station in Søborg, Denmark. Customers and interested companies are invited to attend proof-of-concept demonstrations at the facility. Furthermore, GEA will discuss how to make spray drying plants more sustainable in a webinar featuring the GEA AddCool.
GEA Webinar: “Time is up for fossil fuels in spray drying”
Wednesday, October 26, 2022