MPI Quick Clean Drawer Magnet
Frank Reda, MPI — Magnetic Products, Inc.
Many bulk solids manufacturing operations use magnetic separators to remove ferrous metal contaminants from material during processing to ensure product quality, protect consumers and prevent damage to downstream equipment. Ferrous metal contains iron, making it magnetic, and may enter the material stream in a number of ways at any stage during the manufacturing process.
A magnetic separator uses magnets to remove ferrous contaminants from the flowing material stream during processing. The magnets attract and hold contaminants passing over or near the separator. The captured contaminants then accumulate on the separator until they are cleaned off either manually or automatically.
Many factors influence magnetic separator selection. These include the size of the contaminants you are trying to capture; your material’s characteristics such as bulk density and abrasiveness; and the specifics of your process such as the material flow rate and temperature. These factors can add up quickly and make choosing a magnetic separator confusing and overwhelming.
This information explains the basics of magnetic separators to help you sort through these factors and select the best separator for your application. To ensure the best results; however, you should always work closely with a magnetic separator supplier with experience and expertise in a wide range of bulk solids handling applications.
Magnetic separators can be configured in a number of ways. Common configurations include tube, grate or drawer separators; plate separators; pulley separators; and drum separators. A tube, grate or drawer separator uses one or more magnetic tubes placed directly in the material stream. Because material comes into direct contact with this type of separator, the magnetic field’s strength is concentrated at the magnet surface to hold contaminants once they have been captured.
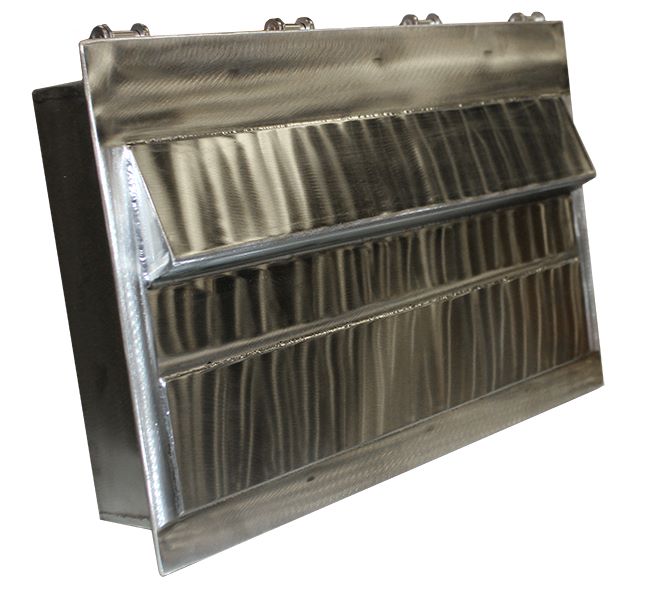
A plate separator is a magnetic plate that is typically mounted inside a chute with the magnetic field’s strength concentrated away from the magnet surface. As material slides down the chute, the magnetic field “reaches out” into the flowing material, attracts ferrous contaminants to the magnet and collects them on the plate.
A pulley separator is a magnetic roll that is used as the head pulley for a belt conveyor. The pulley attracts ferrous contaminants and separates them from the material during belt discharge. Clean material is thrown forward off the belt to the downstream process while tramp metal is drawn around the pulley and discharged beneath the conveyor.
A drum separator is a rotating magnetic drum that is placed directly in the path of a falling material stream. As the material passes over the rotating drum, any ferrous contaminants are captured on the drum surface, rotated out of the flow stream and discharged into a collection container.
The best separator configuration for your application depends on your material’s characteristics and your process. Free-flowing materials will typically flow well through a grate or drawer style magnetic separator, but cohesive materials may bridge across the openings between the magnets stopping flow and causing production delays. With materials that have a high bulk density or processes that have a high flow rate, flowing material can wash off contaminants that have already been captured by the magnets and reintroduce the contaminants to the material stream, so magnetic strength is critical. Abrasive materials can wear through the magnets’ protective steel cover if the steel is too thin, so abrasive applications require a thicker steel layer to avoid having to frequently replace the magnets.
Learn more about magnetic separator solutions at www.mpimagnet.com.