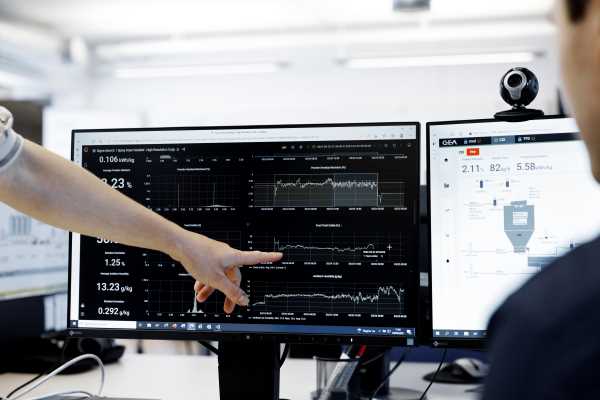
When the beverage industry gathers for Drinktec in Munich from September 12 to 16, 2022, raw material shortages, soaring energy costs, climate change and consumer trends will ensure plenty of buzz. GEA will be presenting technical and digital solutions to help the industry build sustainable, resilient production processes. GEA demonstrates how it is possible to configure hybrid, highly adaptable production lines that enable smaller batches, faster changeovers and greater product variety. (GEA in hall A3, booth 373)
“Considering the almost unparalleled impact that social developments are having on the beverage market, Drinktec could not have come at a better time,” says Ilija Aprcovic, Division CEO of Liquid and Powder Technologies at GEA. “The good news is that GEA is here to help our customers overcome these hurdles. That’s why, at Drinktec, we will be showcasing how we fit out plants to improve efficiency and sustainability as well as respond to consumer trends.”
GEA innovations save water in beverage production
In keeping with the GEA Group’s overarching climate goals, the innovations featured at the trade show will address a critical issue in beverage production – water consumption – and span water recovery and treatment in industrial processes through to water neutrality. By 2030, GEA aims to develop solutions, in particular new cleaning technologies, that do not require the use of drinking water.
- Virtually eliminating freshwater from dealcoholization: The GEA filtration specialists have rounded out the GEA AromaPlus membrane-based beer dealcoholization unit with a sustainable option. GEA AromaPlus PRO drastically reduces the volume of water required during dealcoholization. At the same time, beverage producers can use the by product, the alcoholic base, to produce other alcoholic beverages such as hard seltzer – or reuse it in the brewing process.
- Halving cleaning water consumption in membrane filtration plants: Given that water consumption during cleaning in place (CIP) is a pain point for the beverage industry, the fact that the GEA SmartFiltration Flush intelligent software solution cuts the fresh water used in CIP flushing processes by 50 percent is a real gain. Instead of scheduling a predefined plant cleaning cycle, sensors continually monitor the water’s permeate quality and terminate the cleaning process as soon as the appropriate level of hygiene is achieved. What’s more, numerous customer trials prove that SmartFiltration Flush benefits the CIP system as a whole. Since piping dimensions are based on water volume, the new tool facilitates a more compact CIP design. Added to this is a new, efficient CIP software: GEA Smart Filtration CIP means that the pumps are operated in a pulsating rather than continuous mode. As a result, they consume 50 to 60 percent less power during the CIP process.
- Reducing the cost and resources needed to cool separators: Another new feature, the GEA Centrifuge Water Saving Unit, has already proven its cost-saving potential at a dairy and a brewery. With a quick retrofit, the cooling water needed for the separation process can be reduced by several hundred liters per operating hour. And thanks to its very small footprint, the unit is easily accommodated in the production room.
A big-picture approach on safeguarding resources
GEA enables customers to achieve their climate targets and meet ever-increasing regulations around emissions, water consumption and waste disposal by taking a more big-picture approach to processes. While the GEA technology experts put every component and parameter under the microscope during process planning, GEA never loses sight of a plant’s high-level workings.
- To ensure plants – either new or existing – are sustainable, GEA applies its Sustainable Engineering Solutions or SEnS approach. This enables production plants to be designed as low-energy or even CO2-neutral, while taking into account other parameters such as packaging, water consumption, and potential side streams, etc. GEA successfully implemented SEnS for juice customer, innocent, which recently built its first climate-neutral juice factory in Rotterdam.
- Just as it is possible to recover heat, carbon dioxide from brewery or distillery fermentation can also be reused. In parallel with the industry’s climate protection efforts, CO2 pricing for emitters makes the search for a CO2-reusing technology urgent. This idea is also gaining traction as a result of the Ukraine crisis that makes it almost impossible to source the industrially manufactured gas, which is a byproduct of feed production. Using the GEA CO2 recovery solution helps producers to reuse CO2 instead of emitting it and to make a virtue out of necessity. On the other hand, manufacturers enjoy not only a secure supply for carbonization but also the high purity levels that their fermentation tanks deliver, which is key to the quality of the end product. With stripping technology, GEA can recover even food-grade CO2 from early stages of fermentation. Distilleries, for example, that can recover CO2 from fermentation but cannot use it in their own products, gain an attractive by product for further sale.
Greater flexibility for the beverage industry with hybrid production lines
Shifting supply and demand dynamics and economic pressures are forcing manufacturers to shorten development times for new products. This makes equipment flexibility and productivity key priorities for sustainable beverage production. A lesson learned from the coronavirus pandemic is that manufacturers who can flexibly produce other beverages are better insulated against slumps in demand. GEA’s approach to holistic engineering concepts as well as just-in-time production capabilities helps to prepare for the growing trend toward high dynamics.
For breweries that already have a brewhouse for producing the sugar base and technology for fermenting, blending, carbonating as well as bottling, any expansion is possible. One example of the flexibility of GEA equipment is the GEA AromaPlus membrane dealcoholization unit, which reduces the alcohol content in beer to <0.0 percent. This plant is also used for other non-alcoholic beverages such as 0.0% cider. At the same time, the resulting alcoholic base can serve as the basis for hybrid products, in this case trendy beverages containing alcohol, which run just-in-time through a GEA DICON inline blending plant. The portfolio is rounded out by the multifunctional GEA Visitron Filler ALL IN ONE, which meets the demand for short changeover times for containers.
Digital plant monitoring and autonomous optimization
- GEA supports beverage manufacturers on the digital transformation journey. Together with big-name breweries, GEA has developed the GEA InsightPartner Brewery software, which captures real-time process management data, monitors production performance and alerts users to deviations. If necessary, brewers can quickly take remedial action in order to streamline the brewhouse and cold block over the long term. In a second step, the results of an energy analysis i are integrated with the software, allowing breweries to find the right balance between product quality and quantity and sustainability.
- Long term, GEA is working toward providing producers with an autopilot. That would allow breweries, for instance, to optimize processes in the same way as dairy farmers currently do with the GEA OptiPartner. The process software automatically optimizes process lines in real time, with the result that energy requirements are permanently minimized. Using an interactive user interface, the tool not only provides KPIs that make production line conditions fully transparent but also automatically analyses and regulates efficiency and productivity. Thanks to remote monitoring at a GEA Service Center, users enjoy a lasting improvement in plant availability and performance.
Juice industry trends: natural processing and reduced sugar content
The COVID-19 pandemic triggered a rise in demand for vitamin-rich, immune-boosting vegetable and fruit juices that is set to last for years to come. Experts predict that the market’s annual growth potential in the years leading up to 2026 will be around five percent [1]. Reason enough for GEA to showcase at Drinktec two juice industry innovations that respond to the trends in minimal processing and low-sugar products.
- The GEA Better Juice Sugar Converter Skid is the world’s first solution that naturally reduces juice’s sugar content by up to 80 percent, without affecting its nutritional value or authentic taste. Israeli start-up Better Juice invented the biological process, while GEA designed and built the pilot-scale process technology. Since July 2022, beverage producers can implement product testing with the bioreactor skid at GEA’s test center in Ahaus, Germany.
- Booth space at Drinktec will also be dedicated to the GEA vaculiq 100 juicer, which processes fruit and vegetables to create virtually unadulterated, high-demand drinks. The mobile system is a great choice for small to medium-sized beverage and food producers who want the finished juice to be almost indistinguishable from the fresh raw ingredients. Tests prove that juices produced using the patented process via a vacuum spiral filter retain the raw fruits’ vitamins and phenols to a significant degree, a quality that other juicing technologies cannot achieve. In this way, both the primary and the valuable secondary plant components are preserved. At Drinktec, GEA will present the complete system consisting of the vacuum juicer GEA vaculiq and the powerful GEA multiCrush mill, which efficiently crushes the raw material and feeds the mash into the juicer in the shortest possible time.
Innovative separators for producing beer, wine and other beverages
- GEA aims to serve craft brewers with the new-generation plug & win separator series that will be on show at Drinktec. Equipped with an integrated direct drive and twin hydrohermetic sealing, the GEA plug & win i is more efficient than conventional motors. And thanks to its convenient replacement concept, maintenance is quick. GEA’s newly developed twin hydrohermetic sealing further enhances product quality and safety by preventing oxygen pickup while conserving energy.
- In addition, GEA is rounding out its GSE line of beverage separators with the mid-sized 190-liter unit. Depending on the application, the GEA GSE 190 clarifies 600 hectoliters of beer or up to 27,000 liters of wine per hour. This centrifuge is now also equipped with the energy-saving twin hydrohermetic seal.
“Although sustainability, efficiency and digitalization are becoming increasingly intertwined, this should not be regarded as a Gordian knot,” says Aprcovic in summary. “We are devising technical solutions that leverage smart tools, mechanical engineering and plant design to give our customers a greater competitive edge and achieve broad environmental goals. At GEA, we believe that technology has the innovative power to propel entire industries forward. Our mission is to make that a reality.”